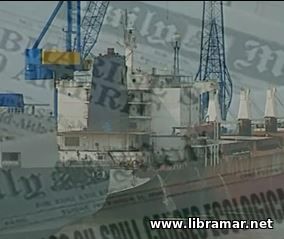 The basic inspection regime for all the MOUs is the IMO conventions. These include the Load Lines, SOLAS, MARPOL, STCW, COLREG and Tonnage conventions. Some MOUs also examine compliance with the relevant ILO conventions. Ships can check each MOU’s website for the further requirements. Complications can arise because for all members of MOUs, their national legislation will take priority over the MOU agreements.
MOUs have different levels of inspection. The initial inspection usually takes about three hours. If there are clear grounds to concern, it may progress to a more detailed inspection, adding another hour or two. Ships with a poor inspection history may be subject to a more detailed inspection. If the Master believes that port state control inspection is likely, he should double check the gangway watch. An ineffective or absent gangway watch will start the inspection badly as it implies poor compliance with the ISM Code. A proper gangway watch must always be in place. The ISPS Code must be strictly kept to. Ships with high target scores, such as old bulk carriers, passenger ships, oil tankers and gas and chemical carriers, will be subjected to an expanded inspection which will take six to eight hours.
MOUs have different levels of inspection. The initial inspection usually takes about three hours. If there are clear grounds to concern, it may progress to a more detailed inspection, adding another hour or two. Ships with a poor inspection history may be subject to a more detailed inspection. If the Master believes that port state control inspection is likely, he should double check the gangway watch. An ineffective or absent gangway watch will start the inspection badly as it implies poor compliance with the ISM Code. A proper gangway watch must always be in place. The ISPS Code must be strictly kept to. Ships with high target scores, such as old bulk carriers, passenger ships, oil tankers and gas and chemical carriers, will be subjected to an expanded inspection which will take six to eight hours.
Under the Paris MOU, the ship is obliged to inform the port if it believes that it is due for the mandatory annual inspection. The Paris MOU website lists the types of ship for which this is required. Always ensure that the PSC officer is escorted to the Master’s cabin. Be aware that the inspector will be looking around to see the state of the ship.
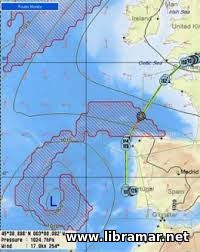 What is voyage planning, who is responsible, how do we comply with the rules and how do we utilize the features and functions available in an ECDIS? The purpose of voyage planning is to support the bridge team and ensure that the ship can be navigated safely between ports from berth to berth. A voyage plan should cover ocean, coastal and pilotage waters and according to STCW regulations be planned in advance. The voyage plan aim to establish the most favorable route while maintaining appropriate margins of safety and safe passing distances offshore.
The following factors are amongst those that should be taken into account:
- - The marine environment
- - The adequacy and reliability of charted hydrographic data along the route
- - The availability and reliability of navigation aids, coastal marks, lights and radar conspicuous targets for position fixing along the route
- - The type of cargo can influence route selection
- - Any routing constraints imposed by the ship, e.g. draught, type of cargo, etc.
- - If possible, avoid areas with dense traffic
- - Take into account weather forecasts, current, tide, wind, swell and visibility conditions
- - If possible, avoid areas with onshore set or areas where onshore set can be expected
- - Whenever possible, follow traffic separation schemes and follow ship reporting procedures
- - Check technical systems before departure and if possible, take into account previous experience of their reliability
- Take into account your own experience with the planned route and type of ship.
There are four main stages in the planning of a safe voyage: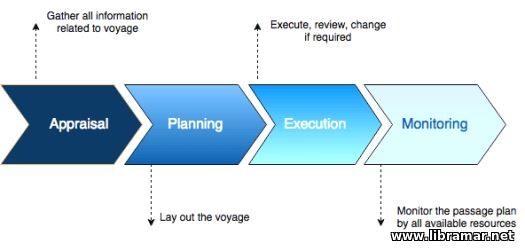
- - Appraisal, i.e. the collection of information and validation of all relevant information;
- - Planning, i.e. the presentation of the raw data -into information and the strategy to be used;
- - The execution of tracking, voyage and communication control;
- - Monitoring, i.e. ensuring that the voyage plan is being followed.
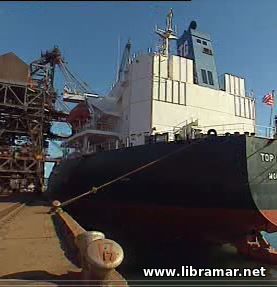 Cargo operations are probably the most important ship operations. They vary enormously from petrochemicals where the discharge is controlled by the ship’s officers to containerships where the discharge and loading is organized and largely carried out by the shore stuff. From your training and experience you will know the requirements of your own ship’s cargo operations but, whatever the cargo, many of the principles remain the same.
Prompt and accurate reporting of any damage must be done within twenty-four hours. Cargo condition, speed of loading or discharging, any delay in operations all can have commercial consequences. The chief officer will know what is critical in your cargo operations and you should discuss the procedures with him. Much of the time cargo operations proceed according to pre-determined plan. It is when the unexpected occurs that the skill of the deck officer is really tested. By responding in the right way you can make a big difference to the commercial performance of your ship.
Make sure you know what can go wrong, what to do and whom to contact if it does. Good situational awareness is the basis for any effective response. Make sure you know what is going on at all times in port. This means being on deck most of the time, keeping your eyes open and communicating with the terminal staff. This will also help with another major task – making sure that the ship is safe.
Current, tide and the cargo operations can all move the ship in relation to the shore if the mooring ropes are slack. The ropes need to be checked regularly for tautness. If your ship has self-tensioning winches, these are best left on the brake and not left in tension once the ship is secured alongside. In an emergency, never release the brakes and attempt to pull a ship back alongside using the power of the winches alone. You must know the ship’s mooring equipment and be familiar with its operation and capabilities including the type of winch and brake, the size, type and length of lines.
Make sure you are aware of the tidal changes and keep an eye on a weather forecast. Sudden changes can have a big impact on cargo operations and additional mooring arrangements may be needed. Be aware of nearby ship movements, check the lines after any ship has arrived or left the next berth.
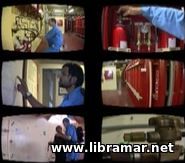 An engine room fire broke out on a tug involved in the towing of an offshore rig and the engine room was believed to be unmanned. The carbon dioxide system panel was opened, the alarm sounded and the engine room ventilation shut down. It took some time to confirm that the engineering specialist on board was not in the engine room. After this delay, it was decided to use the carbon dioxide system. In the stress of the situation, the officer who ordered to operate it forgot the instructions. He believed he was looking at the operating system with the backup. He only operated the first lever. Hours later, he realized he had not operated the system correctly. He decided to check the carbon dioxide room – it was obvious that no carbon dioxide actually reached the engine room. By then, the fire has burned itself out, completely destroying the engine room.
It is vital for the officers to be familiar with the carbon dioxide installations on board their ship; during a major emergency is a wrong time to work out how to use the system. Officers will be faced with demanding decisions. They must educate themselves about the system before they have to use it. If the engine room is on fire and unmanned, the carbon dioxide should be used as soon as possible. There is no benefit in delay. Fire team should only enter the burning engine room if there are personnel inside. Delaying using the system only increases the damage to the engine room or cargo space and increases the risk to the ship and personnel on board.
Carbon dioxide makes up a tiny proportion of the atmosphere, less than 0.1%. At higher concentrations it is not just asphyxiating – it is toxic. It affects the central nervous system – this begins at the concentration of 2% which after an hour or two causes headaches and difficult breathing. A concentration of 5% causes headaches, difficult breathing and sweating. The 10% concentration quickly cases unconsciousness, increased heart rate, headache and sweating. Concentrations exceeding 17% result in loss of control, unconsciousness, convulsions, coma and death.
In dealing with carbon dioxide systems remember that the hazard is much greater that asphyxiation by an inert gas. Although all systems will be different, they will have similar components. These will include a number of gas bottles, a manifold linking them all, and the release system involving main release valve. The release system will always be operated by small gas bottles as these systems are designed to operate without electrical power. There are always two operating systems – one in the carbon dioxide room and remote one outside it but not in the engine room. Two officers should be involved in the releasing of carbon dioxide...
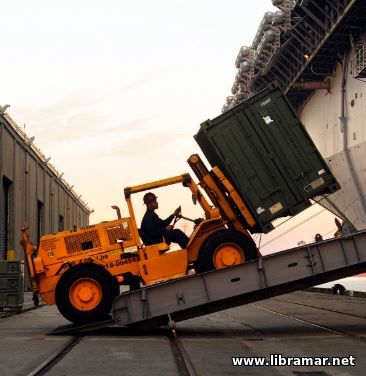 As we know, the forklift trucks are among the most useful and practical devices used on board ships. However, they shall be used with utmost care since they can be really dangerous to the people. The first thing is to assess the risk – a standard operating procedure for the use of forklift will have been produced as a result of the general risk assessment. This procedure should identify the hazards associated with operating the equipment on board particular vessel. It will also contain the control measures, such as the use of the correct personal protection equipment.
Only the qualified drivers shall be allowed to drive the truck. They shall have completed the appropriate training course conducted by the authorized organization. The certification they achieve shall be kept on boast as part of their personal records. Never use a forklift truck if you are not qualified to operate. And, prevent anyone from operating a forklift truck, who is not qualified or authorized to use it. Under no circumstances should you operate the forklift truck if you are taking prescribe medication affecting your ability to drive.
Likewise, anyone found driving under the influence of alcohol or illegal substances, is liable for immediate company dismissal and possibly criminal prosecution from port state authorities. In some instances, the work permit may be issued. This is good practice as it creates the record of the forklift truck use and the people who are authorized to drive it. The ignition key is then handed over. Note that they must be removed from the ignition each the forklift truck is left unattended or stowed.
A number of checks shall be made before the forklift truck is used. Firstly, we shall ensure the good working condition of the device. Ideally, there should be a condition checklist supplied based on the manufacturers guidelines, and the technical inspection should take a minimum of 5-10 minutes; that five or ten minutes of your time well worth taking – it will ensure the safety of yourself and your colleagues. These checks shall be made in the following order. Firstly, is the parking brake on? Next, the cage should be checked; where the open top cages are fitted, the hard hats must be worn as necessary.
It is recommended to always wear a hard had with the chin strap in place when operating the any forklift truck. The safety belt, if fitted, should be tested and inspected for wear – this must be worn at all times whilst driving the vehicle. Check the hydraulic connections for any leaks and wear-and-tear. The load guard, carriage plate, and forks should be inspected for signs of cracks or deficiencies. Oil and fuel levels must be checked. The oil level is correctly established by taking a dip stick reading. Coolant levels are checked and any relevant hoses inspected. There should also be sufficient fuel in the tank for the day’s operations. Wheels and tires are examined. Only now and upon completion of all checks, should the engine be started. If the engine fails to start, under no circumstances should the attempt be made to jump start the vehicle.
Once started, the foot brake can be tested. The steering should be checked for excessive play or wear. See and be seen – vehicle lights and hazard lights must work efficiently and any mirrors positioned correctly by the driver. Be heard – check the horn and any reversing alarms. The hydraulic controls also need to function correctly. Finally, the tilt mechanism is tested. If any deficiencies are found, report must be made to the officer-in-charge and the key is returned, and “Do not use” sign must be displayed clearly so that the other crew members are aware of its condition. Remember, no matter how often it is used, each time the forklift truck is signed over, it must be checked prior to use.
It must be established that the forklift truck is capable of lifting the load safely. At no time should you lift the load greater that than the vehicle’s specified Safe Working Load, which must be clearly marked. Care should be applied to the establishing the weight of the items to be lifted or moved. Large items, such as machinery or equipment, should also have their own weight indicated. Stores shall have their weight clearly described on the packaging or the delivery note. Never attempt combined lift with another vehicle. Complicated lifts involving a pair of forklifts requires special training and should not be carried out by ship’s personnel. Stores and supplies are usually delivered to the ship on pallets and these are ideally for maneuvering the loads around easily.
Whenever possible, put items on the pallets and secure them. The condition of the pallet must be checked for damage or defects before use. Items should be placed centrally on the pallet to maintain even balance. Larger pieces of equipment which are not suitable for palletizing, can be moved safely so long as they are secured and within the SWL of the equipment. Waste containers and the garbage bins are often moved by forklift trucks. Some of them are designed for this purpose; others are not and should be carried on a pallet. In some instances, forklift truck will be as the raised work platform – never use a pallet for this operation, only use specially designed, certified and approved man carrying cages.
All working aloft procedures must also have an appropriate risk assessments carried out and permits issued prior to use. A forklift truck is not a taxi – under no circumstances should the cage be used to transport crew members. Particular attention must be given to how the forks interact with loads. Pallet sizes vary. The distance between the slots must correspond correctly with the forks. If not, the forks will need to be adjusted. Fork plates must be leveled and spaced equally apart, equidistant from the center to avoid a potentially dangerous unbalanced load. The load must also be checked for fork blade length. If the load exceeds the length of the forks, it could topple forward. If the load is significantly shorter that the fork length, the protruding blades must be taken into account, particularly if there are other pallets nearby. Remember – only lift items that can be moved or carried safely within the working limits.
It is vital that the fellow crew members, stevedores, visitors or anyone else in vicinity are aware of the forklift operations taking place. Extreme care should also be taken of passenger on vehicle ferries. Pedestrian walkways, emergency exits must remain clear. Ro-Ro loading and discharge involve a constant stream of traffic arriving and leaving the ship. Caution must be observed to avoid collision with the vehicles. Extra care must be taken if the load has to be reversed. If the load is large and obscures the vision of the driver, second crew member may be required to act as a signaler and to control the traffic flow, if necessary. Access to either the pickup point or drop off point should be checked for obstructions.
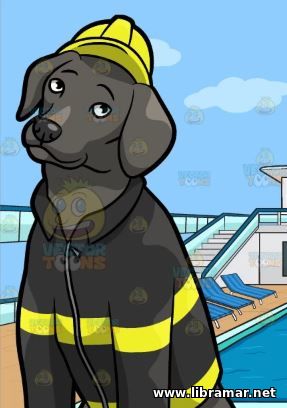 No matter how well designed the rig or how well supervised the crew, only careful, conscientious conduct by everyone can assure safe operations. Each person should receive instructions on the proper way to perform their work and the use of personal protection equipment (PPE). Safety standards prohibit the wearing of rings or other jewelry, loose clothing, or long hair on a drilling rig. All these things are subject to being caught in moving machinery.
The mandatory personal protection items worn by each crewman should include hard hat, safety boots, gloves, and safety glasses. Proper clothing is also important.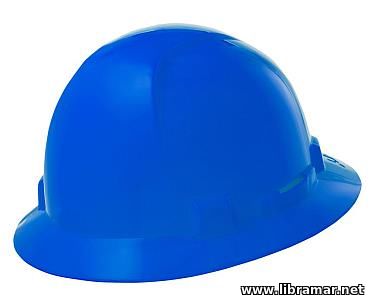
Hard Hat
Safety hard hats must be worn by all personnel, including visitors, when in the work area. Hats must be of nonmetallic, nonconductive material. They must meet prescribed standards of strength and protection from impact, flying objects, or electrical shock. A bright colour increases visibility.
Safety Shoots and Boots
Steel-towed footwear made of heavy leather or neoprene construction is mandatory on drilling rigs. They greatly decrease the number and severity of toe injuries. Soles and heels should be of nonskid material (rubber is too slippery). They should be discarded when the metal begins to show.
Gloves
Gloves protect the hands from minor injuries and improve the hold on slick or wet surfaces. They should be of heavy cotton construction, short and close fitting. Large gauntlets are apt to get caught in something so gloves of this type should not be worn. Rubber gloves are needed when handling caustic or corrosive material.
Safety Glasses, Goggles, Face Shields
Eye protection is of utmost importance. If an eye injury occurs, prompt medical attention is critical. Personnel should always wear approved safety glasses, goggles, or face shields when engaged in the activity where flying material is generated. These should be readily available on every rig. The risks to eyes are numerous, whether engaged in routine maintenance chores or a major activity like pulling the drill string. Any action involving a hammer can produce flying chips. Wire brushes, grinding wheels, scraping, compressed air or steam cleaning operations all present dangers to vision.
Approved splash-proof goggles or face shields should be worn when handling hazardous materials, such as caustic, cement, cleaning solutions, molten metal, or chemicals of any kind.
Electric arc welding operations should be shielded to prevent damage to the eyes of observers. The welder should always have a helmet on and helpers should be furnished special goggles.
Contact lenses are discouraged because they can hinder attention to the eye if immediate action is required.
Clothing
Only close-sitting, clean clothing should be worn. Long-sleeve shirts, with shirttails tucked in, are recommended. Cuffless trousers help prevent tripping. Each crewman should have available a fresh change of clothing should their work clothes become oily or soaked with chemicals. Aprons should be worn when handling chemicals.
In cold weather, dress as lightly as possible considering the weather and activity level. It is better to be a little cold than too warm. Overheating can cause sweating, dehydration, and chilling when activity stops. Keep clothing as dry as possible and wear the clothing in layers. Sweaty or wet socks can lead to frostbite or trench foot; change them often.
Specialized Equipment
Hearing protection gear should be worn around any high noise area, such as around the rig engines.
Respirators are required for spray painting, mud fixing, or working in heavy dust. Special breathing equipment and instruction are needed if hydrogen sulfide is, or may be, present.
Falls cause a significant number of injuries; therefore, a full-body safety harness is required for anyone working or climbing aloft six feet or more above the derrick floor.
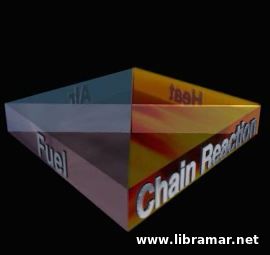 In the previous article we have talked about the common sources of fire and now let’s talk about fire extinguishing. The key to extinguishing any fire is first to control it, then the flame area can be minimized and finally the fire extinguished. It is important to understand the four components that sustain the fire – fuel, air, heat, and the chain reaction. If any of these can be removed, the fire will cease. As a result, there are four ways to fight fire. The most important is to starve the fire of fuel by shutting off supply; next is to choke off the air supply. Cooling through evaporation is essential to limit the spread of fire. Once the other elements are in place, it is possible to break the chain reaction at the source of ignition.
There are four technologies available to fight the fire. To starve the fire of fuel, there are emergency systems to shut valves and stop pumps. There are passive systems, such as melt plugs on deck which activate shutdown systems at around 100 C, there is remote control through the product management system and there is ability to shut off fuel by closing valves manually. Enclosed cargo machinery spaces are provided with the fixed fire extinguishing systems suitable for the cargo carried to smother the fire. However, it is important to evacuate spaces before they are used. CO2 released at pressure can cause ignition through static electricity so it must only be used to extinguish fires and never be used to inert spaces not on fire.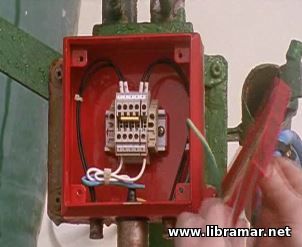
Outside, the key to smothering is high expansion foam. While rarely successful in extinguishing liquefied gas fires unaided, foam is invaluable in reducing the rate of burning of pool fires in drip trays and bounded areas. Once again, if the fire is to be got under control, it is essential to reduce the radiant temperature rapidly. Foam acts to reduce the vapor emission. And, if the vapor is unignited, helps minimize the risk of ignition. Large amounts of foam are required. For LNG and LPG the foam, if available, should be optimized to create a blanket to minimize vaporization through insulation and by reducing contact with air. By its nature, foam is ineffective against jet fires.
Water is the most effective medium for cooling. Gas containers are deluged to reduce the evaporation rate due to the heat of the fire. Large volumes of water may be supplied by firefighting tugs. Water is used to reduce damage to pipes and valves, to protect personnel operating valves, or to create a barrier to prevent the fire spreading from vessel to shore. Water can also be used to disperse gas, but it does not normally extinguish the fires unless the gas can be dispersed by water spray at high volume and pressure. However, water must be used with care, especially where liquid gas has pool – in such case its effect may cause liquid to boil faster and make the fire more difficult to control.
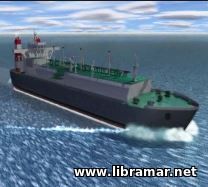 Gas - LNG, LPG, methane, propane, butane - all valuable products compressed, or cooled, into liquid to make it hundreds of times smaller. It is transported safely in more than a thousand vessels around the world. It is safe when contained. But, when it escapes, it mixes with air with such low flash points and all it takes is a small source of ignition. It the fire is not contained rapidly, the results are potentially catastrophic.
Fire - four letters to describe very serious problem, four letters to describe the solution. Find It - Inform - Respond - extinguish. Finding a fire is relatively simple. But better still to detect escaping gases before they ignite. The problem is that both LPG and LNG are odorless and colorless. However, as the vapor is cold, it will cause a visible mist and will flow downhill like water. But the flammable gas cloud, especially with LPG, may extend well beyond what can be seen, and any flame will travel back to the source.
There are important differences between LPG and LNG vapor. LPG is heavier than air so it flows downhill and stays on the ground. LNG initially flows downhill and then rises as it heats up. So, the ignition risks for each may be different.
The IMO IGC Code specifies that vessels must have fixed detection alarms set at no more than 30% of the lowest flammable limit in the enclosed areas such as cargo, machinery rooms, accommodation blocks etc. Some systems are designed to shut down automatically at 60% LFL. Terminals also have vapor and fire detection systems and their firefighting and mitigation systems will be installed according to local requirements.
Vessel crew and terminal staff should keep each other fully informed about any fire or potential hazard. If you find a fire or ignited gas, it’s important to raise the alarm immediately. The ship’s master or terminal manager will then inform those who need to know, such as the fire brigade and the port authority. Most vapor emissions and liquefied gas spills do not result in fire. On both terminals and vessels electrical equipment is suitable for use in hazardous areas and should not cause ignition.
Should these mitigation measures fail to prevent ignition, there are two main types of fire that could result - pool fires, which are often in contained areas, and jet fires, which are often caused by a failure of a pressurized valve, a pump or a pipe. Pool fires are normally tackled first as these can cause the failure of pipes and valves, and re-ignite extinguished jet fires.
Respond quickly – time is of the essence in firefighting. Both vessel and terminal start their fire pumps. Deluge systems, water curtains and foam generators are brought into action to restrict the effects of the fire. Water spray can be used for boundary cooling, create a flame barrier or to disperse the vapor cloud.
If one tank is on fire, nearby tanks will be protected with the deluge system. The source of the gas is located and cut off remotely, if possible. Firefighting teams are mustered and correct PPE including BA’s is prepared. Hoses are run out and crew is moved to the firefighting positions. Now comes the crucial decision, whether to extinguish or control burning and then extinguish.
The decision taken will depend on individual circumstances such as whether the fire is heating vulnerable machinery, pipes, valves, or storage. Will heat damage these and create further gas or liquid escapes? Which is the greater danger – extinguishing and allowing unignited gas top escape, or allow the fire to burn? Often unignited gas is more dangerous than fire as in rare instances it could lead to a vapor cloud explosion. How much gas is likely to escape and where will it? This depends on wind strength and whether it will flow over open water or industrial land. Is it likely to disperse harmlessly or pool somewhere? Potential ignition sources downwind should be considered, such as vessels, port facilities, and houses. Often, a decision is taken to allow the gas to burn off while the source is isolated. A jet fire in a fractured pipe is likely to provide a different set of challenges and pose different questions about the risks.
If the valve is damaged and vapor cannot be controlled immediately, the water jet can be used to deflect the flame up to ninety degrees away from the vulnerable systems. Care must be taken not to extinguish the flame. Although ignited gas is often safer than unignited gas, deliberately igniting gas can be very hazardous. There is no knowing how far it is spread and where it has pooled. Every second counts - as containment vessels heat up, liquid gas boils creating ever higher pressures. But LNG and LPG boil in different ways - LPG boils off faster making it harder to control.
If, due to flame impingement, the vessel is weakened and the pressure builds within the tank beyond the point where the pressure release valve can cope, it’s possible to have a boiling liquid expanding vapor explosion. When unignited vapor is confined, or contained, it is also possible to have a vapor cloud explosion.
There are other important differences between these gases. LNG is stored at -162 degrees – it is so cold it can crack steel plates and cause severe frostbite. It can also reduce the effectiveness of protective clothing. It also burns very cleanly, with less visible flame. Its greater radiant heat makes to more difficult to get close to the source of the fire.
Whether the fire is caused by LNG or LPG, the surfaces heat up beyond 200 degrees Celsius and water droplets are deflected by the steam layer and so become less effective. The longer the fire has to create heat, the more difficult becomes controlling it. So, all firefighting equipment and clothing should be stowed for rapid access, and staff must be aware of its location…
To be continued...
|